1. Introduction to ATEX Zone Classification
Overview of ATEX Regulations
The ATEX (Atmosphères Explosibles) directives are European Union regulations designed to ensure the safety of environments where explosive atmospheres may occur. These regulations, particularly Directive 2014/34/EU and Directive 1999/92/EC, are pivotal in defining and managing hazardous areas within various industries, including oil and gas, chemical, and food processing sectors. ATEX Zone Classification is integral to these directives, providing a framework to identify, assess, and mitigate risks associated with explosive atmospheres.
Importance of ATEX Zone Classification in Safety
The classification of ATEX Zones is not merely a regulatory requirement but a critical component of workplace safety. Proper classification ensures that risks related to explosive atmospheres are effectively managed, preventing catastrophic incidents that could lead to loss of life, property damage, and environmental harm. The precise identification of hazardous areas enables the implementation of appropriate safety measures, including the selection of suitable equipment and the development of emergency response plans.
Purpose of This Guide
This guide aims to provide a comprehensive understanding of ATEX Zone Classification, offering detailed insights into the methodologies, standards, and practices involved. It is designed for professionals tasked with ensuring compliance with ATEX regulations, such as safety officers, engineers, and plant managers, offering practical guidance on how to classify hazardous areas effectively.
2. Understanding ATEX Zone Classifications
What is ATEX?
ATEX is an acronym derived from the French term “Atmosphères Explosibles.” The ATEX directives regulate the safe use of equipment and protective systems intended for use in explosive atmospheres. They encompass a wide range of industries where gases, vapors, or dust can create potentially explosive environments.
History and Evolution of ATEX Directives
The ATEX directives have evolved to address the growing complexity and diversity of industrial processes. Initially introduced in the 1990s, these directives have undergone several revisions to incorporate technological advancements and to respond to incidents that have highlighted the need for stricter safety regulations.
Legal Requirements and Compliance
Compliance with ATEX regulations is mandatory within the European Union including the UK. Non-compliance can result in severe penalties, including fines, legal action, and the suspension of operations. Companies must adhere to both the ATEX 114 Directive, which governs the manufacturing and sale of equipment, and the ATEX 137 Directive, which pertains to the protection of workers.
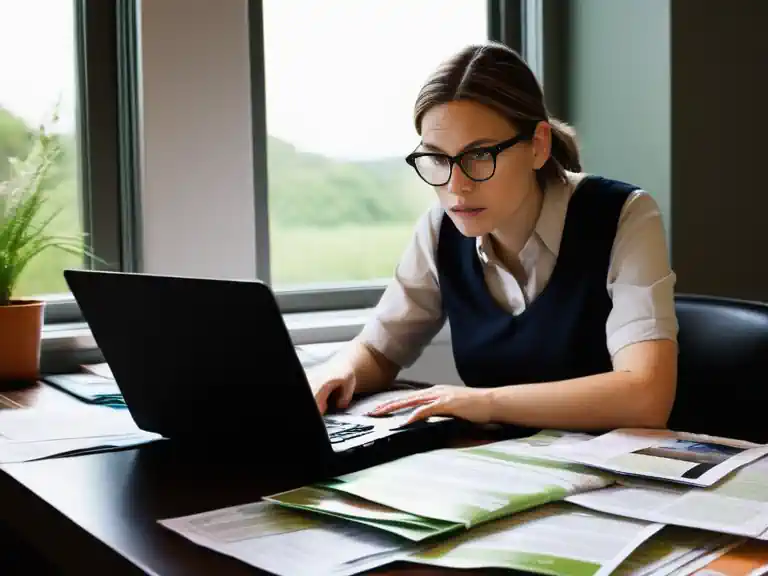
3. The Basics of Hazardous Area Classification
Definition of Hazardous Areas
A hazardous area is defined as any environment where explosive atmospheres are likely to occur. These atmospheres can be the result of flammable gases, vapors, mists, or dust mixed with air. The classification of these areas is crucial to ensure the safety of personnel and the protection of property.
Types of Hazards: Gas, Dust, and Vapors
Hazards in explosive atmospheres are generally categorized into three types:
- Gas Hazards: Arise from the presence of flammable gases such as methane or propane.
- Dust Hazards: Occur when combustible dust, like grain or metal dust, is suspended in the air.
- Vapor Hazards: Created by the evaporation of volatile liquids like gasoline or solvents.
Importance of Correct Classification
Incorrect classification of hazardous areas can lead to inadequate safety measures, increasing the risk of explosions. Proper classification ensures that all potential sources of ignition are identified and controlled, and that appropriate equipment is used in each area.
4. ATEX Zones Explained: A Detailed Breakdown
Understanding ATEX Zone Numbers
ATEX Zones are numerical designations that indicate the likelihood and duration of explosive atmospheres in a given area. These numbers help in determining the level of risk and the corresponding safety measures required.
Differentiating Between Gas and Dust Zones
ATEX Zones are further divided based on the type of hazardous substance present:
- Gas Zones (0, 1, 2): Relate to the presence of flammable gases, vapors, or mists.
- Dust Zones (20, 21, 22): Concern environments where combustible dust is present.
Common Misconceptions About ATEX Zones
Misunderstandings about the classification of ATEX Zones can lead to improper implementation of safety protocols. For example, some may assume that Zone 2 (gas) and Zone 22 (dust) are inherently safer than Zones 0 and 20, overlooking the specific conditions that can make them equally hazardous.
5. Classifying Hazardous Areas: A Step-by-Step Guide
Identifying Potential Sources of Ignition
The first step in classifying hazardous areas is to identify all possible sources of ignition. This includes both internal sources, such as electrical equipment, and external sources, like open flames or hot surfaces.
Evaluating the Frequency and Duration of Hazardous Atmospheres
Next, assess how often and for how long explosive atmospheres are present. This involves analyzing operational processes, environmental conditions, and historical data to determine the likelihood of an explosive atmosphere occurring.
Documentation and Reporting Procedures
Once the hazardous areas have been classified, it is essential to document the findings thoroughly. This documentation should include the rationale behind the classification, the methods used, and the safety measures implemented. Proper reporting ensures that all stakeholders are informed and that regulatory requirements are met.
6. Detailed Definitions of Zone 1 and Zone 2
Characteristics of Zone 1 Areas
Zone 1 is an area where an explosive atmosphere is likely to occur during normal operations. This zone is common in industries where flammable gases or vapors are routinely present, such as chemical plants or refineries. Equipment used in Zone 1 must be certified for use in such environments.
Characteristics of Zone 2 Areas
Zone 2 is defined as an area where an explosive atmosphere is unlikely to occur under normal operating conditions but, if it does occur, it will only persist for a short period. This zone is often found in areas adjacent to Zone 1, where leaks or spills could create a temporary hazardous atmosphere.
Practical Examples of Zone 1 and Zone 2 Applications
- Zone 1 Example: A chemical reactor vessel where flammable gases are regularly present during production.
- Zone 2 Example: The area surrounding the storage tanks in a refinery, where gases may escape during filling operations.
7. Gas & Dust Zones: Understanding the Differences
Zone 0 vs. Zone 20: Continuous Presence of Hazardous Substances
Zone 0 and Zone 20 are areas where an explosive atmosphere is present continuously or for long periods. These zones require the highest level of safety precautions due to the constant presence of hazardous substances.
Zone 1 vs. Zone 21: Likely Presence of Hazardous Substances
Zone 1 and Zone 21 are areas where an explosive atmosphere is likely to occur during normal operations. These zones require robust safety measures but are generally less hazardous than Zones 0 and 20.
Zone 2 vs. Zone 22: Infrequent Presence of Hazardous Substances
Zone 2 and Zone 22 are areas where an explosive atmosphere is not likely to occur under normal operations but may happen occasionally. These zones are considered the least hazardous but still require appropriate safety measures.
8. Explosive Atmosphere Classification: Key Concepts
Defining an Explosive Atmosphere
An explosive atmosphere is a mixture of air and flammable substances in the form of gases, vapors, mists, or dusts that can ignite under certain conditions. The classification of explosive atmospheres is crucial for determining the appropriate safety measures.
Factors Contributing to Explosive Atmospheres
Several factors contribute to the formation of an explosive atmosphere, including the concentration of the flammable substance, the presence of oxygen, and the temperature and pressure conditions.
How Explosive Atmospheres are Classified
Explosive atmospheres are classified based on the type of hazardous substance present and the likelihood and duration of its occurrence. This classification helps in determining the necessary safety precautions and the selection of suitable equipment.
9. Zones 0 & 20: High-Risk Areas
Specific Characteristics of Zone 0 and Zone 20
Zone 0 and Zone 20 are considered the highest risk areas within ATEX classifications. In these zones, an explosive atmosphere is present continuously or for long periods, making them extremely hazardous. Equipment used in these zones must be of the highest safety standard, often requiring intrinsic safety (IS) or explosion-proof (Ex) certification.
Examples of Environments Classified as Zone 0 and Zone 20
- Zone 0 Example: Inside a fuel storage tank, where flammable vapors are constantly present.
- Zone 20 Example: A silo containing fine combustible dust, such as flour or coal dust.
Safety Measures and Precautions for High-Risk Zones
Due to the high risk associated with Zones 0 and 20, stringent safety measures are necessary. These include:
- Using certified equipment with appropriate ATEX ratings.
- Implementing rigorous maintenance and inspection protocols.
- Ensuring strict control over potential ignition sources.
10. Zones 1 & 21: Moderate-Risk Areas
Identifying Moderate-Risk Environments
Zones 1 and 21 represent environments where the risk of an explosive atmosphere is moderate, typically occurring during normal operations. These zones require significant safety precautions, although the level of risk is lower than in Zones 0 and 20.
Safety Guidelines for Zone 1 and Zone 21
- Equipment Selection: Use equipment certified for use in Zone 1 or 21, ensuring it meets the necessary ATEX standards.
- Operational Controls: Implement operational controls to minimize the release of hazardous substances.
- Regular Monitoring: Conduct regular monitoring of the environment to detect any changes that could increase the risk of an explosion.
Case Studies of Zone 1 and Zone 21 Applications
- Zone 1 Case Study: A distillation column in a petrochemical plant where flammable vapors are regularly present.
- Zone 21 Case Study: A dust extraction system in a grain processing facility where combustible dust is frequently present.
11. Zones 2 & 22: Low-Risk Areas
Characteristics of Low-Risk Zones
Zones 2 and 22 are classified as low-risk areas where the presence of an explosive atmosphere is unlikely and, if it does occur, will only last for a short duration. Despite the lower risk, it is still crucial to implement appropriate safety measures to prevent accidents.
Operational Protocols for Zone 2 and Zone 22
- Equipment Usage: Use equipment that is suitable for Zones 2 or 22, with a focus on ensuring that it does not create any ignition sources.
- Preventive Maintenance: Conduct preventive maintenance to reduce the likelihood of hazardous substances being released into the environment.
- Emergency Preparedness: Develop and rehearse emergency response plans specific to Zone 2 and 22 scenarios.
Managing Risks in Low-Risk Environments
Even in low-risk zones, it is essential to manage risks effectively. This involves continuous assessment of potential hazards and ensuring that all safety systems are functioning correctly.
12. Defining ATEX Zones: Methodologies and Approaches
ATEX Zone Mapping Techniques
Mapping ATEX Zones involves creating a visual representation of the hazardous areas within a facility. This process helps in identifying the boundaries of each zone and ensuring that appropriate safety measures are implemented across the entire facility.
Criteria for Zone Classification
Several factors determine the classification of ATEX Zones, including the type of hazardous substance, the likelihood of its presence, and the duration of exposure. These criteria must be carefully evaluated to ensure accurate zone classification.
Tools and Software for Accurate Zone Mapping
Various tools and software are available to assist in the mapping and classification of ATEX Zones. These tools help streamline the process, ensuring that all relevant factors are considered and that the classification is both accurate and compliant with regulatory standards.
13. ATEX Zone Classification Guidance: Best Practices
Common Challenges in Zone Classification
Classifying ATEX Zones can be challenging due to the complexity of industrial processes and the variability of environmental conditions. Common challenges include:
- Identifying All Potential Ignition Sources: Overlooking minor sources can lead to incomplete classifications.
- Evaluating Dynamic Environments: Environments that change over time can complicate the classification process.
- Maintaining Compliance: Ensuring that classifications remain compliant with evolving standards and regulations.
Strategies for Accurate and Consistent Classification
To overcome these challenges, it is essential to adopt a systematic approach to zone classification. This includes:
- Involving Experts: Engage with experienced professionals who understand the nuances of ATEX regulations.
- Using Reliable Tools: Leverage advanced tools and software to assist in the classification process.
- Regular Reviews: Conduct periodic reviews of zone classifications to ensure they remain accurate and up-to-date.
Role of Industry Standards in Zone Classification
Industry standards, such as IEC/EN 60079-10-1, provide a framework for ATEX Zone Classification. These standards offer guidance on the criteria for classification, ensuring that all relevant factors are considered and that the classification is consistent with industry best practices.
14. ATEX Zone Mapping: Creating an Accurate Representation
How to Develop a Zone Map
Developing a zone map involves several key steps:
- Data Collection: Gather data on the types of hazardous substances present, their concentrations, and the environmental conditions.
- Risk Assessment: Conduct a thorough risk assessment to identify potential hazards and determine the likelihood of an explosive atmosphere occurring.
- Zone Delineation: Use the collected data to delineate the boundaries of each zone, ensuring that all areas of potential risk are accurately represented.
Factors to Consider in Zone Mapping
When creating a zone map, consider the following factors:
- Source of Hazard: Identify the source of the hazardous substance and its potential impact on the surrounding environment.
- Ventilation: Assess the ventilation in each area, as this can significantly affect the likelihood of an explosive atmosphere forming.
- Proximity to Ignition Sources: Ensure that zones are classified with respect to their proximity to potential ignition sources.
Case Examples of ATEX Zone Maps
- Example 1: A chemical plant where Zone 0 is mapped inside a reaction vessel, Zone 1 around the vessel, and Zone 2 in adjacent areas.
- Example 2: A grain processing facility with Zone 20 inside the storage silos, Zone 21 in the dust extraction areas, and Zone 22 in surrounding areas.
15. Zone Classification Methodology: A Structured Approach
Step-by-Step Guide to Classifying Zones
- Identify Hazardous Substances: Start by identifying all hazardous substances present in the facility.
- Assess Risk Factors: Evaluate the factors that could lead to the formation of an explosive atmosphere.
- Determine Zone Boundaries: Based on the risk assessment, determine the boundaries of each ATEX Zone.
- Select Appropriate Equipment: Choose equipment that is certified for use in the classified zones.
- Document the Classification: Ensure that the classification is thoroughly documented and communicated to all relevant stakeholders.
Involving Key Stakeholders in the Classification Process
Effective zone classification requires the involvement of key stakeholders, including safety officers, engineers, and management. Their input is critical in ensuring that all aspects of the classification are considered and that the process is aligned with the facility’s overall safety strategy.
Validation and Verification of Zone Classifications
Once the zones have been classified, it is essential to validate and verify the classification. This involves reviewing the classification against industry standards, conducting site inspections, and testing safety systems to ensure they are functioning as intended.
16. ATEX Zone Classification Standards: IEC/EN 60079-10-1
Overview of IEC/EN 60079-10-1 Standards
The IEC/EN 60079-10-1 standards provide comprehensive guidelines for the classification of hazardous areas. These standards are widely recognized and adopted across various industries, offering a consistent approach to ATEX Zone Classification.
Application of Standards in ATEX Zone Classification
Applying these standards ensures that the classification process is both rigorous and compliant with regulatory requirements. The standards cover all aspects of zone classification, from identifying hazardous substances to determining the appropriate safety measures.
Compliance Requirements and Best Practices
Compliance with IEC/EN 60079-10-1 is essential for ensuring the safety of personnel and the protection of assets. Best practices include regular training for staff, continuous monitoring of hazardous areas, and periodic audits to ensure ongoing compliance.
17. Identifying ATEX Zones: A Practical Guide
Techniques for Identifying ATEX Zones
Several techniques can be used to identify ATEX Zones, including:
- Hazard and Operability Study (HAZOP): A structured approach to identifying potential hazards in a process.
- Layer of Protection Analysis (LOPA): A method for assessing the effectiveness of existing safety measures.
- Fault Tree Analysis (FTA): A top-down approach to identifying the potential causes of an explosive atmosphere.
Tools and Resources for Identification
Various tools and resources are available to assist in the identification of ATEX Zones, including:
- ATEX Compliance Software: Tools that help streamline the classification process and ensure compliance with regulatory standards.
- Guidelines and Best Practices: Industry guidelines that provide detailed instructions on how to classify hazardous areas.
Common Pitfalls in Zone Identification
Common pitfalls in zone identification include:
- Overlooking Minor Hazards: Failing to consider small or infrequent sources of ignition can lead to incomplete classifications.
- Inaccurate Data Collection: Inaccurate or incomplete data can result in incorrect zone boundaries and inadequate safety measures.
- Inadequate Training: Without proper training, personnel may not fully understand the classification process or the importance of accurate zone identification.
18. ATEX Zone Determination: Key Factors to Consider
Assessing Hazardous Substances and Sources
The first step in ATEX Zone determination is to assess the hazardous substances present in the facility. This includes identifying the type of substance, its concentration, and its potential to create an explosive atmosphere.
Environmental and Operational Factors
Environmental factors, such as temperature, pressure, and humidity, can significantly impact the likelihood of an explosive atmosphere forming. Operational factors, including the frequency and duration of hazardous substance release, must also be considered.
Documenting the Determination Process
It is essential to document the ATEX Zone determination process thoroughly. This documentation should include the methods used, the rationale behind the classification, and the safety measures implemented. Proper documentation ensures transparency and facilitates audits and inspections.
19. ATEX Zone Risk Assessment
Conducting a Comprehensive Risk Assessment
A comprehensive risk assessment is crucial in the ATEX Zone classification process. This assessment should consider all potential hazards, including those related to the release of hazardous substances, the presence of ignition sources, and the potential for human error.
Identifying Potential Consequences
The risk assessment should identify the potential consequences of an explosive atmosphere, including injury, property damage, and environmental harm. Understanding these consequences helps in determining the appropriate safety measures.
Implementing Mitigation Measures
Based on the risk assessment, implement mitigation measures to reduce the likelihood and impact of an explosive atmosphere. These measures may include the use of explosion-proof equipment, the installation of ventilation systems, and the implementation of strict operational controls.
20. Zone Classification for Safety
The Role of Zone Classification in Workplace Safety
Zone classification plays a critical role in ensuring workplace safety by identifying hazardous areas and implementing appropriate safety measures. Proper classification reduces the risk of explosions and ensures the safety of personnel and property.
Integrating Zone Classification into Safety Management Systems
Integrating ATEX Zone classification into the facility’s overall safety management system ensures that it is continuously monitored and updated as necessary.
How to Do a Thorough ATEX and DSEAR Compliance Risk Assessment
ATEX and DSEAR are regulations designed to protect workers and the public from the risks posed by explosive atmospheres (ATEX) and dangerous substances (DSEAR). Performing a risk assessment is a crucial step in complying with these regulations. Here’s a guide to conducting a thorough risk assessment for ATEX and DSEAR as applies to all businesses in […]
Waste Management Industry Health and Safety Problems – ATEX and DSEAR in Context
Waste Management Industry Health and Safety problems have been mounting, and the industry needs to wake-up to all risks including those from landfill sites and specifically those arising from landfill gas and covered by the UK Dangerous Substances and Explosive Atmospheres Regulations (DSEAR). After a number of recent years when the Waste Management Industry sector […]
Details of New ATEX and DSEAR Website!
This website is provided by IPPTS Associates Environmental Consultancy and experienced DSEAR Risk Assessors since 2011. This website is dedicated to explaining the ATEX Directives and the UK DSEAR (Dangerous Substances and Explosive Atmosphere Regulations). While covering DSEAR compliance for companies operating in the United Kingdom, it provides unique insights into landfill DSEAR risk assessment […]